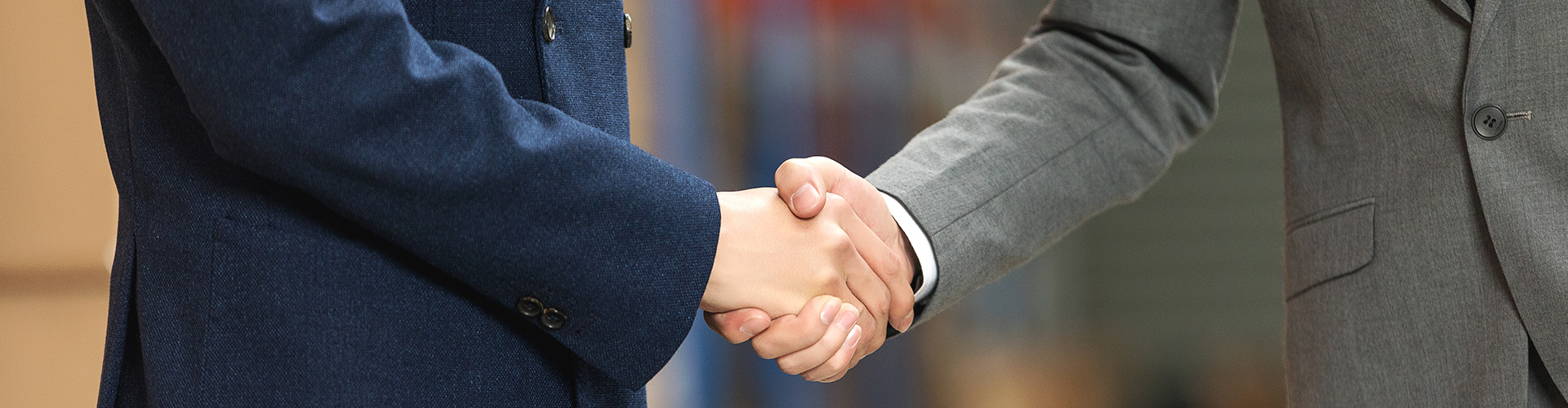

近日,由中国石油天然气股份有限公司牵头承担的国家重点研发计划项目“高性能合成橡胶产业化关键技术”在赛轮(东营)轮胎股份有限公司召开了双B级轮胎生产示范和长寿命胶囊应用示范现场评估会。
此次评估会由中国石油和化学工业联合会组织,与会专家考察了轮胎制造生产线及长寿命胶囊应用示范现场,听取了中国石油天然气股份有限公司、怡维怡橡胶研究院和赛轮(东营)轮胎股份有限公司的应用生产示范汇报。
评估认为,采用中国石油独山子石化分公司工业生产的官能化溶聚丁苯橡胶和稀土顺丁橡胶,浙江信汇新材料股份有限公司工业生产的溴化丁基橡胶,分别应用于轮胎胎面、胎侧和气密层,并通过采用自主开发的原位补强湿法混炼技术、低温一次法炼胶工艺、电子辐照交联工艺生产的225/55R16规格轮胎,经西班牙IDIADA Automotive Technology SA检测,滚动阻力及抗湿滑性能分别达到欧盟轮胎标签法规A级和B级。
采用自主开发的长寿命硫化胶囊配方和制备工艺技术批量化生产的产品,经第三方用户使用证明,平均使用寿命622次;经专家在赛轮(东营)轮胎股份有限公司现场考察,使用寿命达610次以上。
双B级轮胎生产示范和长寿命硫化胶囊应用示范是继官能化溶聚丁苯橡胶、窄分布稀土顺丁橡胶、溴化丁基橡胶、星型支化丁基橡胶4种高性能合成橡胶工业生产示范后的橡胶应用示范,也是该项目的最后一项产业化生产应用示范,标志着此国家项目中所有工业生产示范工作圆满完成。
双B级轮胎生产示范采用的官能化溶聚丁苯橡胶、稀土顺丁橡胶、溴化丁基橡胶全部由项目组自主开发。至此,项目完成了4个高性能合成橡胶材料小试、中试研究及工业生产示范,并定型3个工业产品牌号,开发高性能轮胎及长寿命硫化胶囊制造技术2项,不仅实现了轮胎工业用关键核心基础材料的国产化,也实现了国产轮胎用关键核心基础材料制备国际一流轮胎产品的突破,将使我国高性能轮胎用关键基础材料平均占比提高15%以上,轮胎达到双B级及以上,年节油550万吨,引领国内合成橡胶及轮胎产业链的全面升级。
文章出处:转载【《中国化工报》社有限公司】,本文章版权归原作者及原出处所有,内容为作者个人观点, 并不代表本网站赞同其观点和对其真实性负责。如涉及侵权或对版权有所疑问,请邮件联系bangguhuaxue@126.com。我们会尽快处理,感谢。